I
contacted the owners of
Evergraph and explained what I
had planned, a couple of days later I delivered both HDPE butcher
blocks to them. They did an absolutely top notch job using a raw
material foreign to the standard, the lithophanes measure 30" tall
each and are awesome.
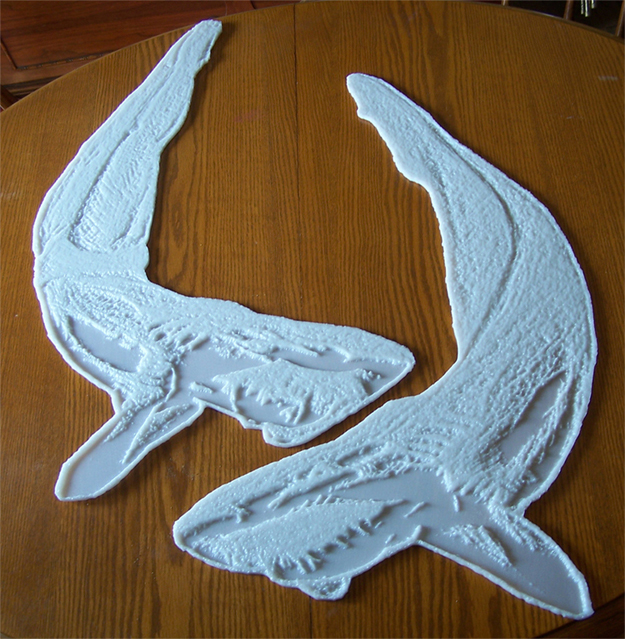
Here
is how they work, hold them up to a light source and they become a
black and white image. The areas where the material is thickest are
dark and the thin areas show whiter as more light shows through.
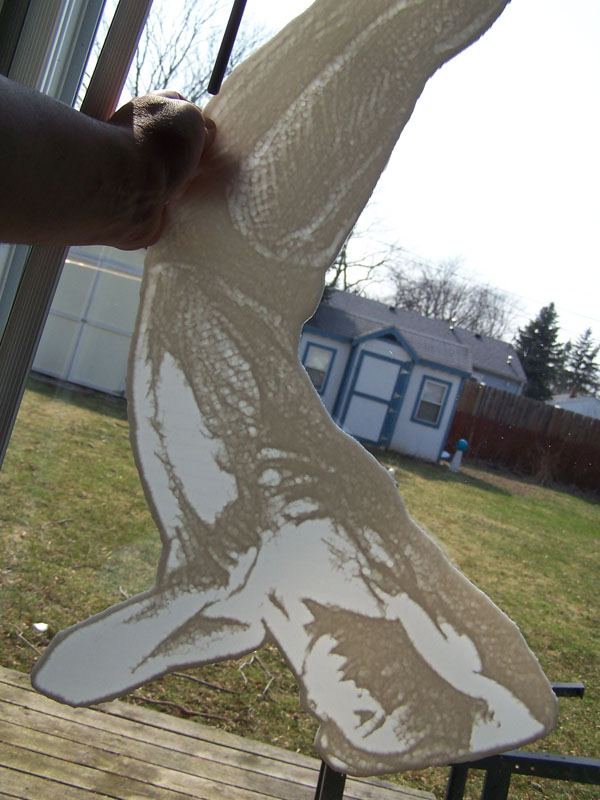
I spent a lot of time trying to figure out how best to illuminate my
lithophanes, but then it occurred to me that I could use a really
expensive large high end HDTV and glue them to the front. I
decided against it because I wanted the TV to be replaceable should
it happen to break but more importantly I could not afford a single
HDTV big enough to accommodate both lithophanes, with that said the
twin 50" 4K panels I chose for the project are shown below.
The
aluminum angle outer framing is cut to fit and bolt holes are marked
for drilling.
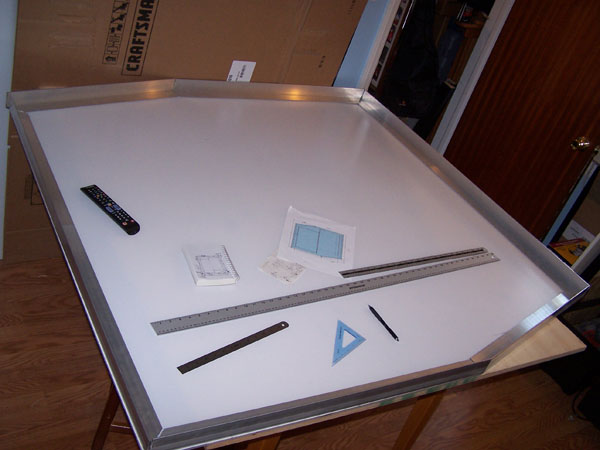
The
outer frame is bolted together and support pieces are installed,
below shows the first test fit and the final placement of the TV's.
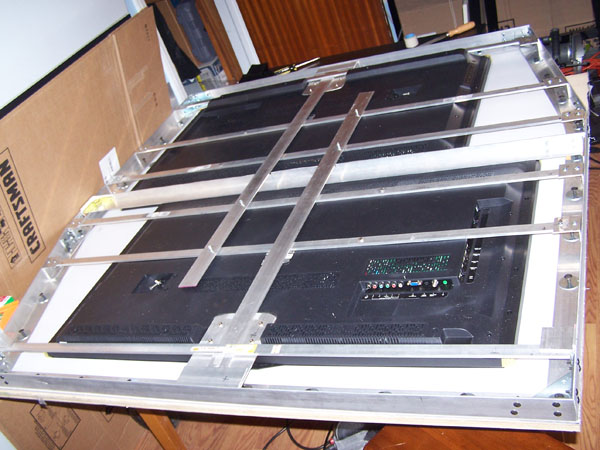
The
aluminum framing was primed and sprayed with several coats of black
Plasti-Dip.
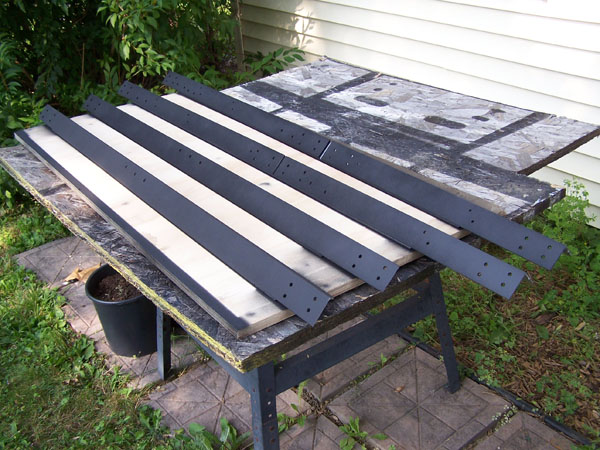
The sheet of acrylic is masked off in preparation for back painting
with black automotive vinyl color.
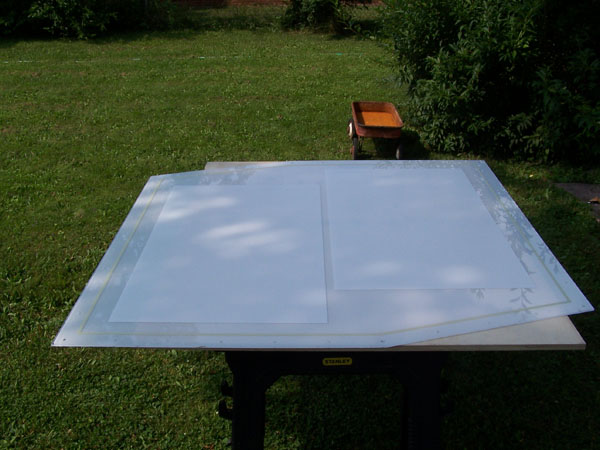
Below shows the finished back painted piece.
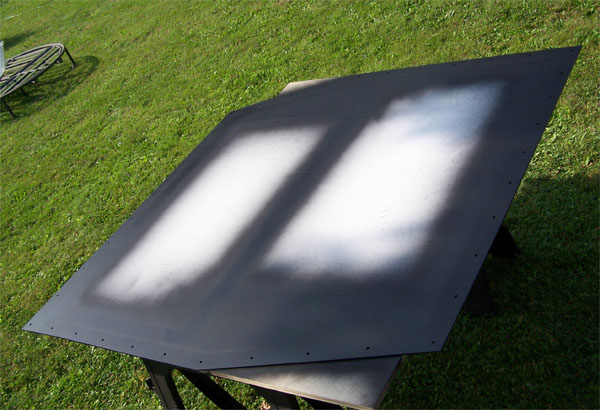
I am
using black oxide carriage bolts to hold this thing together, they
can't attach directly to the acrylic because it would crack so I am
making support pieces and spraying them front and back with black
Plast-Dip.
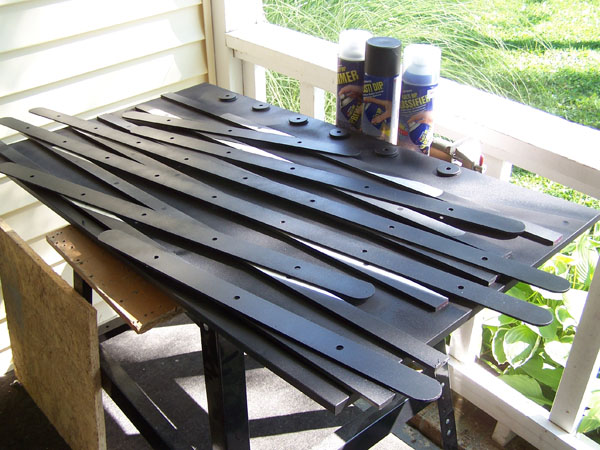
The framing is bolted onto the back painted acrylic and the masking
will be removed.
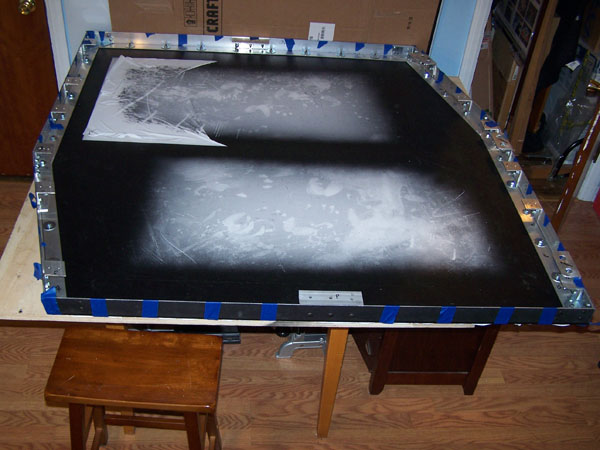
Everything is put together, but it is too heavy for me to flip over
or hang on the wall... I will need help.
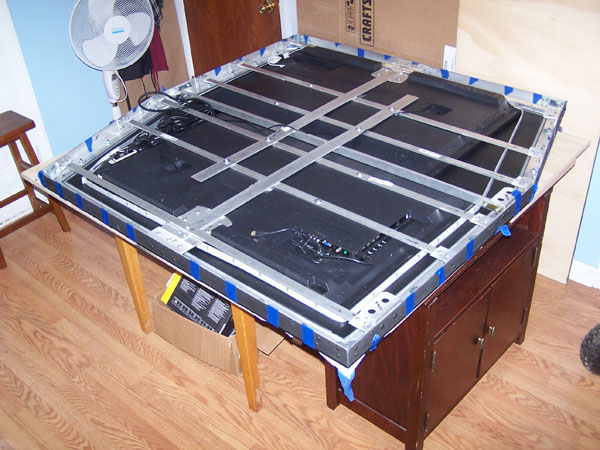
Below is a closer look at the dual row 5050 SMD programmable LED
strip that outlines the work and the controller for it, at sixteen
feet the SMD LED strip made it around both TV's with almost nothing
to spare.
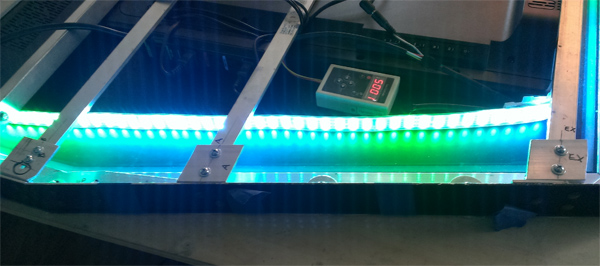
Found help and muscled the 200+ pound work onto my wall, now I see
the flaws. I left a thin line of masking material under the diver
and have mask under the front flat aluminum angle on the shark side
edge.
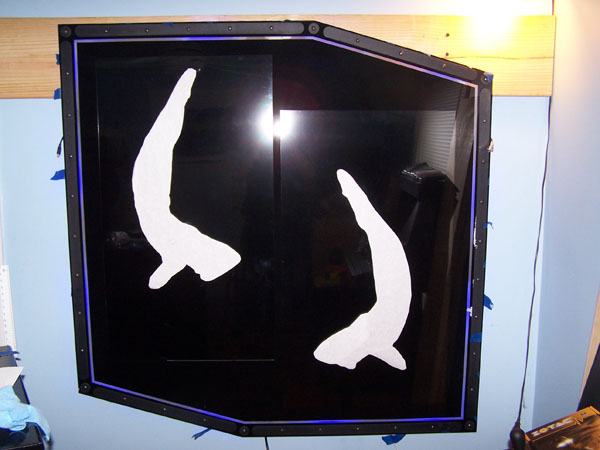
The
whole thing will have to be disassembled and fixed, but again I will
need help to take it back off the wall, in the meantime I can work
on backgrounds.
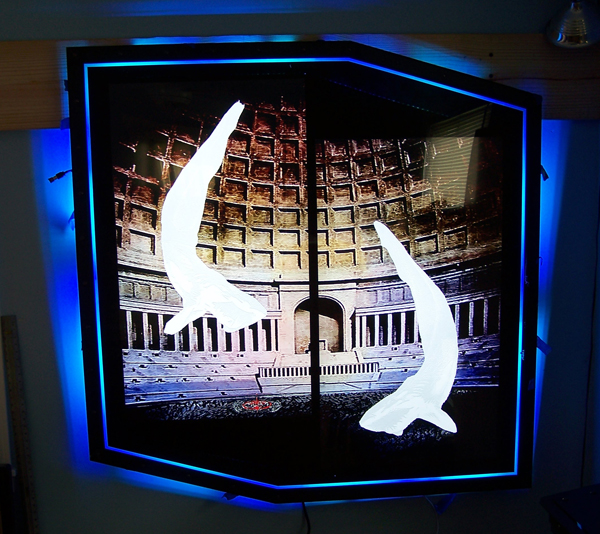
Below is what $115 USD will get you, and that is a good price for
this industrial adhesive from what I was seeing. This is 35 mL of
the only translucent adhesive capable of bonding HDPE to
polycarbonate acrylic and the required applicator gun for it, 10:1 mixing tip and
10:1 plunger.
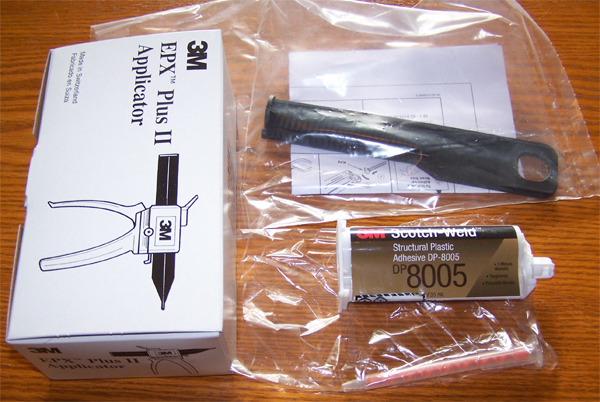
I
quickly installed both lithophanes, since the adhesive only allowed
for a 3 minute work time. After everything fully cured I applied the
olympic ring vinyl decal to the front.
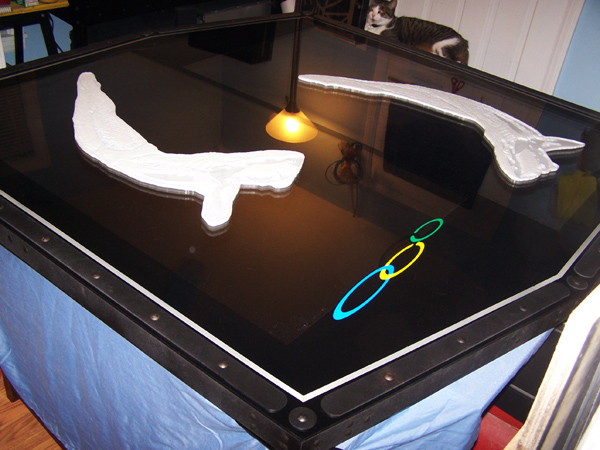
Here's the view from the other side...

Now
with the lights turned down.
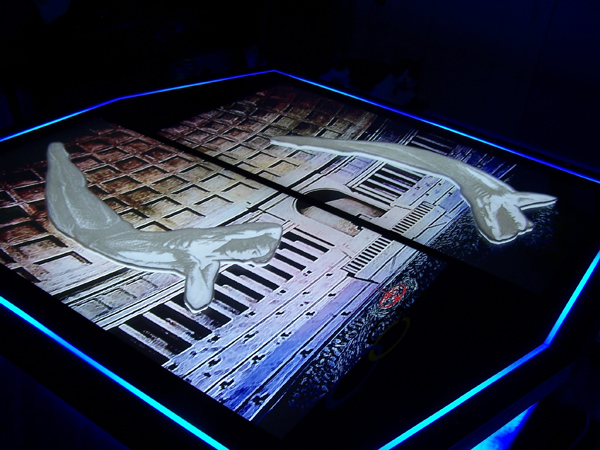
Close up...
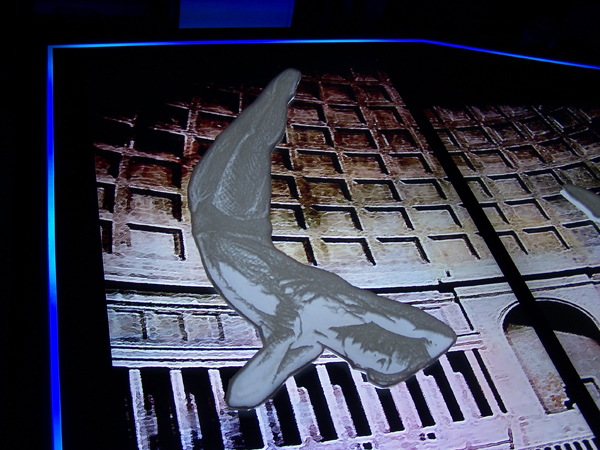
Closer...
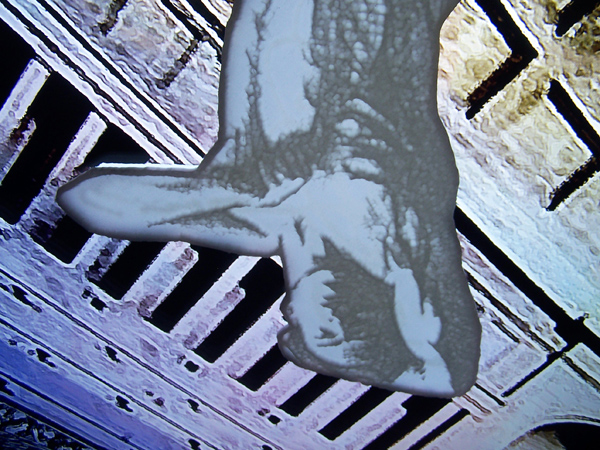
The
shark.
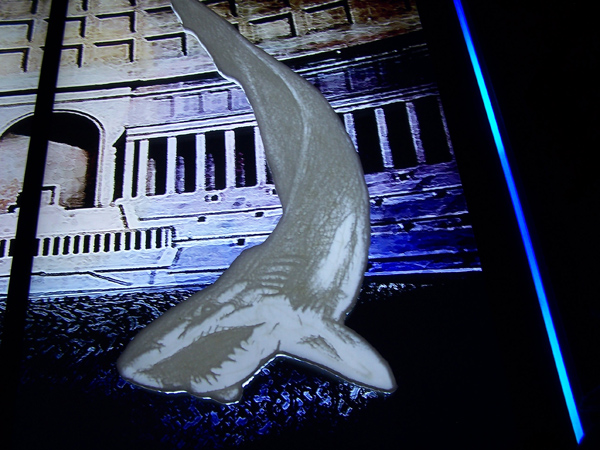
Both
lithophanes...
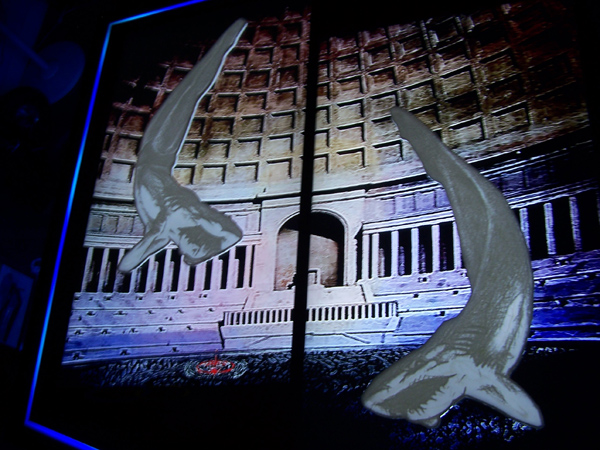
Here
it is freshly installed on the wall at the DeVos Place Convention Center,
if you are in Grand Rapids during ArtPrize come check it out.
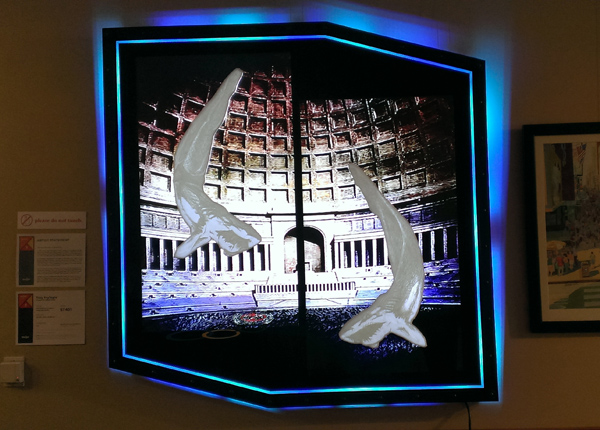
The artist statement that accompanies the work reads as follows:
In 1988 Olympic diver Greg Louganis injured his head on the
springboard and bled into the pool, that same year I began a career
as a butcher. In the image the shark is swimming toward a blood
droplet hitting water, the red ring it forms is detached from the
other four Olympic rings which are floating away forming the number
eighty eight.
My original dual image sketches of the shark and diver were done in
1992, but in this work the paranoiac critical shark is the diver
mirrored with both images CNC carved into lithophanes from an actual
24"x30" white butcher block that I've spent ten plus years cutting
meat on. The four detached Olympic rings are cut from sign vinyl and
exist on the same plane as the lithophanes.
The shark and diver are each illuminated by its own 50" 4K Ultra
High Definition TV showing white silhouettes behind them while also
displaying the digital background image. The piece is subtly
animated by programmable dual LED strip lighting that reflects off
the inner aluminum to simulate rippling water and outline the frame.
Designed using free 3D software and fabricated entirely from scratch
by hand in a small 10'x12' home work shop over the course of six
months, it's built out of back painted polycarbonate sheet acrylic,
black spray rubberized aluminum angle and black oxide carriage
bolts, at 5'x5' it is my largest work to date.
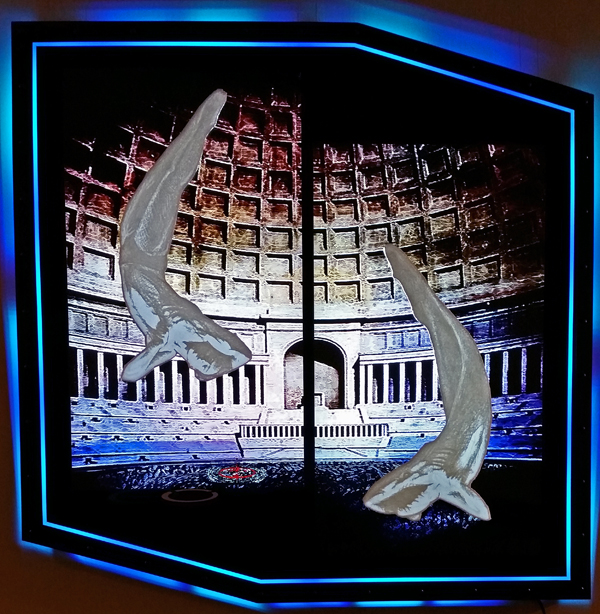